Thermal Conductivity of Duocel® Foam Materials
Overview: Duocel® open-cell foam is a high-performance, engineered material used in thermal management applications across aerospace, electronics, and energy systems. Its thermal conductivity is a function of multiple parallel and interacting mechanisms. The total effective thermal conductivity keff includes contributions from conduction through the solid ligaments, conduction through the contained gas, gas convection, and radiative transfer.
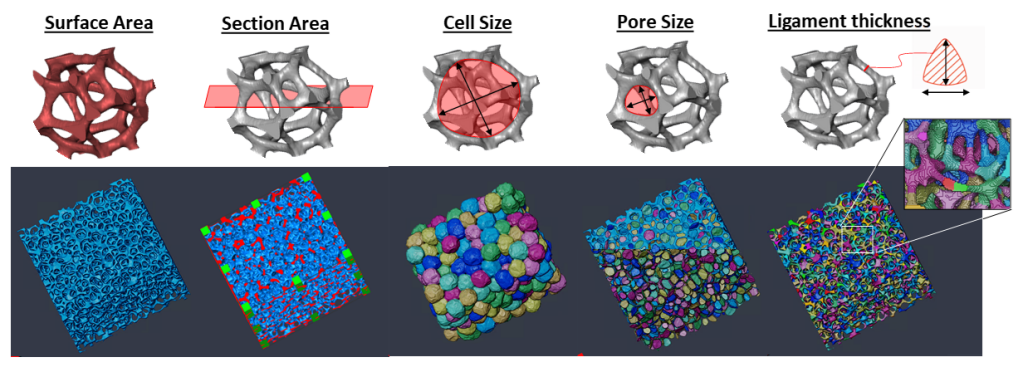
1. General Thermal Conductivity Equation for Open-Cell Foam
keff = ksolid + kgas + kconvection + kradiation
- keff : Total effective thermal conductivity (W/m·K)
- ksolid: Solid-phase conduction
- kgas: Gas-phase conduction
- kconvection: Convection through gas motion
- kradiation: Radiative heat transfer
Note: aluminum and copper foams are typically used for thermal transfer applications. Often, the contributions from kgas, kconvection, and kradiation are considered negligible when calculating overall thermal conductivity for aluminum and copper. (see table below)
2. Solid Ligament Conduction
ksolid = kbulk ⋅ ρ_rel ⋅ τ
- kbulk: Bulk thermal conductivity (W/m·K)
- ρ_rel: Relative density (e.g., 10% = 0.10)
- τ: Tortuosity factor (∼0.33)
Material Values (10% Relative Density):
- Aluminum: 200 ⋅ 0.1 ⋅ 0.33 = 6.6
- Copper: 400 ⋅ 0.1 ⋅ 0.33 = 13.2
- SiC: 150 ⋅ 0.1 ⋅ 0.33 = 4.95
- Carbon: 2 ⋅ 0.1 ⋅ 0.33 = 0.066
Significance of the 0.33 Tortuosity Factor
The 0.33 coefficient is not arbitrary. It arises from both:
- Experimental measurements of electrical conductivity across various foam samples
- Conceptual geometric modeling, where the foam is approximated as a three-dimensional orthogonal array of pin fins
3. Gas Conduction
kgas = kgas, bulk ⋅ (1 − ρ_rel)
- kgas, bulk: Thermal conductivity of the fill gas (e.g., air ≈ 0.026 W/m·K)
Example
(Air, 10% RD): kgas = 0.026 ⋅ 0.9 = 0.0234
Relative Impact:
- Aluminum, Copper: Negligible
- SiC: Minor
- Carbon: Significant
4. Convection
kconvection ≈ 0 (for small pore sizes or vacuum)
Rayleigh number:
Ra = (g ⋅ β ⋅ ΔT ⋅ d³) / (ν ⋅ α)
- g: Gravitational acceleration
- β: Thermal expansion coefficient
- ΔT: Temperature difference
- d: Characteristic pore size
- ν, α: Kinematic viscosity and thermal diffusivity
Suppression Strategy: Use fine-pore foam (80–100 PPI)
Relative Impact:
- Aluminum, Copper: Negligible
- SiC: Minor
- Carbon: Potentially significant
5. Radiative Transfer
kradiative = (16 ⋅ σ ⋅ T³ ⋅ ε_eff) / (3 ⋅ β)
- σ: Stefan-Boltzmann constant (5.67 × 10⁻⁸ W/m²·K⁴)
- T: Absolute temperature (K)
- ε_eff: Effective emissivity
- β: Extinction coefficient (related to pore size)
Typical Emissivity:
- Aluminum: ∼0.1–0.2
- Copper: ∼0.05–0.1
- SiC: ∼0.8–0.9
- Carbon: ∼0.9
Relative Impact:
- Aluminum, Copper: Minor
- SiC, Carbon: Significant at T > 227°C (500 K)
Summary Table (10% RD, Air, 27°C(300K))
Material | ksolid | kgas | kconvective | kradiative* | keff (approx.) |
---|---|---|---|---|---|
Aluminum | 6.6 | 0.023 | 0 | 0.05 | 6.7 |
Copper | 13.2 | 0.023 | 0 | 0.03 | 13.3 |
SiC | 4.95 | 0.023 | 0.05 | 0.3 | 5.3–5.4 |
Carbon | 0.066 | 0.023 | 0.05 | 0.4 | 0.5–0.6 |
* Estimated for T ∼ 500–600 K with typical pore sizes.
Use these equations and values to estimate total thermal conductivity or for input into thermal simulation models. For high-fidelity modeling and design optimization, please contact us.