Why Choose ERG and Duocel® for your project?
Experienced engineering team for foam design included with your project
ERG has designed, developed, and delivered numerous Duocel® foam based products for critical applications. We have the experience and engineering expertise including an in-house test laboratory and database, to precisely adjust the Duocel® parameters to meet the mechanical and performance requirements of your project.
We have amassed a great deal of engineering mastery over the past 50 years, expertise in both designing and manufacturing Duocel® foam metal components. Our engineers can design and optimize Duocel® foam components for performance and manufacturability in a broad variety of applications.
For example, we have detailed thermal models for predicting and optimizing the performance of Duocel® metal foam heat exchangers. We have mechanical properties test data that can be used to calculate and predict the performance of Duocel® foams for impact absorption and structural applications. If you contact us, our engineers can quickly determine if Duocel® foam components would be viable in your particular application.
Duocel® is available in a variety of materials including carbon and metal foams.
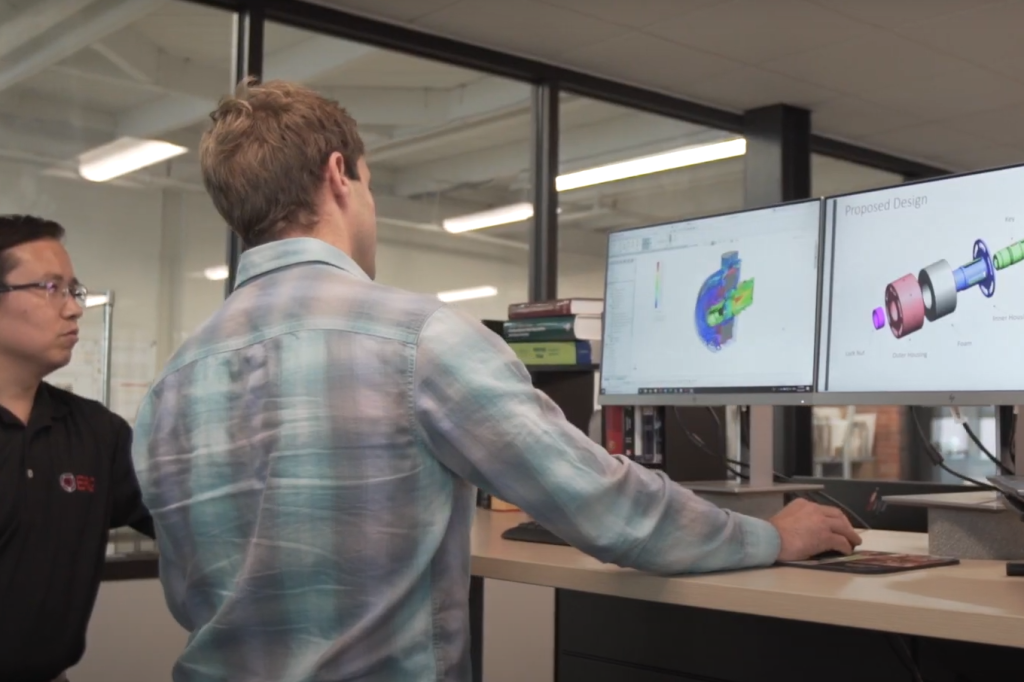
Our foam is available in your custom size and shape
Our dedicated Duocel® foam machine shop covers over 20,000 sq. ft., and is comprised of both manual and CNC machines. Precision machinery coupled with decades of experience by our machinists assures the highest quality Duocel® components and assemblies. Our experience and knowledge in machining open-celled metal foams is unmatched by anyone in the world. We also maintain the unique ability to have our engineering staff co-located in the same building allowing our engineers the flexibility to ensure the Duocel® components meet your required performance criteria.
Duocel® foams are unique materials which require special proprietary fabrication and manufacturing processes that ERG Aerospace corporation has developed over the last 50 years. We work with our customers to define the performance requirements and optimize the Duocel® component design. We then perform the fabrication and machining to ensure the product meets your quality and performance requirements. ERG’s basic and QA systems are based on and certified to AS9100 Rev D, which is the US aerospace version of the international standard ISO 9001. For this reason, we do not sell Duocel® foams in raw or bulk form, but only as finished end item components. This ultimately saves everyone time and money, and results in a superior cost-effective product.
It is possible to bond Duocel® products utilizing conventional epoxies and adhesives. Such bonding agents must be compatible to the Duocel® base material and its finished operating environment. Bonding is considered a cost effective alternative to brazing.
Brazing is common among our thermal management products to increase their heat transfer efficiency. Specialized brazing techniques and processes are necessary to ensure the highest quality in our products.
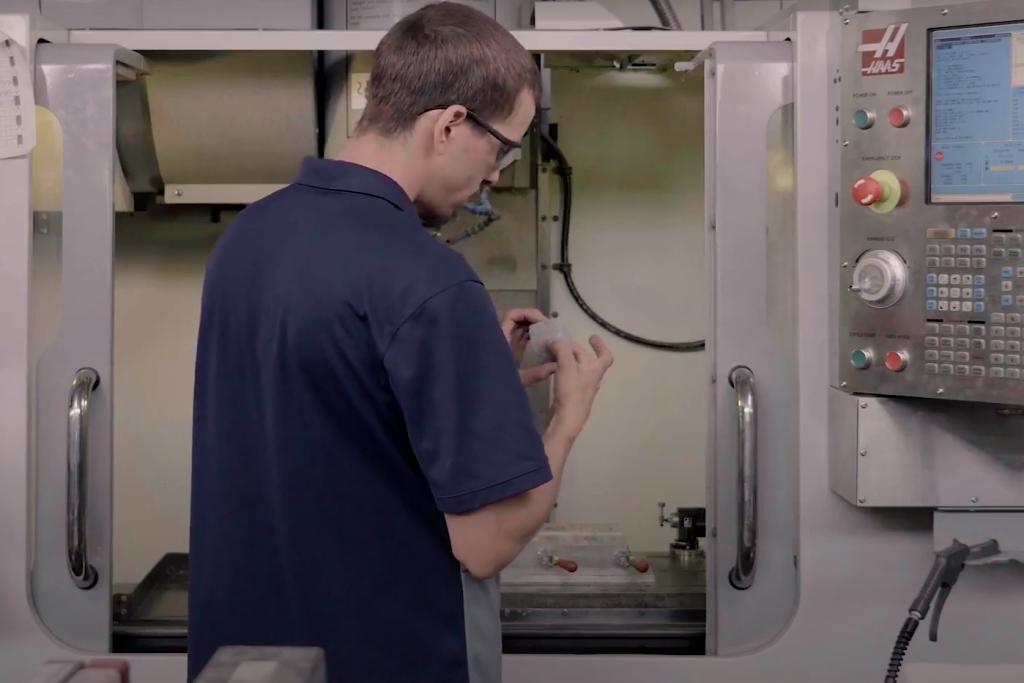
Over 50 years of experience
Founded in 1967, ERG Aerospace Corporation has been manufacturing open-celled, solid ligament metal foams called Duocel®. Since then, ERG Aerospace Corporation has been producing foamed metals, carbons, and ceramics for the aerospace, defense, semiconductor manufacturing, biomedical, and scientific industries.
Up until the mid-1990’s, the majority of ERG’s business was sequestered for military applications and included the design and manufacture of critical foam components for reconnaissance satellites, nuclear weapons, ICBMs, and other aerospace systems. With the end of the Cold War, the advanced design and manufacturing technologies that ERG had perfected were then made available for commercial, scientific, and non-classified military applications.
Service-Disabled Veteran Owned Small Business
ERG is a proud member of the Service-Disabled Veteran Owned Small Business Program
Made in the USA
Our original facility has been in Oakland, CA since 1967In 2017 we added a manufacturing facility in Sparks, NV
On January 1, 2022 ERG officially moved its corporate headquarters to Nevada; the California facility will continue to focus on production, engineering, R&D, and precision manufacturing
AS9100D Certified
Past Performance
2017 – Pratt & Whitney SDVOSB Supplier of the Year2018 – IHI Aeroengines Supplier of the Year
2019 – United Technologies Supplier Gold Awardee
2018 & 2019 – Nevada Manufacturing Excellence Nominee