Can Duocel® foam replace Retimet™ foams?
Yes! For many applications, a replacement foam is available from Duocel®.
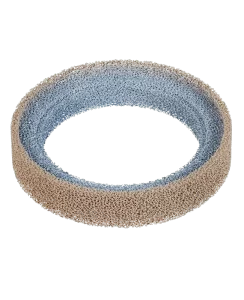
Replacing Retimet™ Foam with Duocel® Foam
What are Retimet™ Foams?
Retimet™ is a brand name for a nickel-chromium alloy foams that have become increasingly difficult to produce due to environmental restrictions. As a result, industries that previously relied on these foams are now seeking alternative materials that provide similar performance characteristics.
Why Choose Duocel® Foam as a Replacement?
Duocel® foams offer comparable properties to Retimet™ without utilizing chromium in the manufacturing process, making them a more sustainable and regulatory-compliant solution. Duocel® foams are also RoHS-compliant, ensuring they meet modern environmental and safety standards.
Depending on the application, we have successfully supplied Duocel® in aluminum, nickel-plated aluminum, Copper, and silicon carbide as replacements for nickel-chromium foam. These materials provide excellent performance in thermal management, filtration, energy absorption, and catalyst support applications.
Primary Retimet™ Applications:
Thermal Management
- Use Case: Heat exchangers and dissipators in environments up to 1250°F ( >850°F requires Copper), particularly in aerospace and industrial machinery.
- Duocel® Replacement: Aluminum, Nickel-plated aluminum or Copper foam for thermal conductivity.
Filtration
- Use Case: Harsh chemical or high-temperature environments where fine filtration and structural integrity are essential.
- Duocel® Replacement: Silicon carbide for high-temperature and corrosive environments.
Energy Absorption
- Use Case: Crash protection systems, impact absorption, or vibration dampening.
- Duocel® Replacement: Aluminum foam or Nickel-Plated Aluminum Foam for lightweight and high-energy absorption efficiency.
Catalyst Supports
- Use Case: High surface area applications, such as catalytic reactions in fuel cells and battery electrodes.
- Duocel® Replacement: Silicon carbide foam for high-temperature stability and chemical resistance. Carbon (RVC) foam is an excellent catalyst support for nonstructural applications as well.
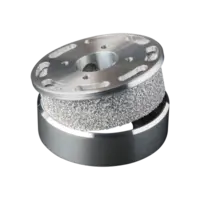
Duocel® Material Options and Advantages
Aluminum Foam
- Best for applications operating below 850°F (450°C).
- Ideal for flow control, impact protection, diffusion, and air-oil separation.
- Lightweight and corrosion-resistant.
Nickel-Plated Aluminum Foam
- Stronger than standard aluminum foam.
- Suitable for higher temperature and structural applications.
- Used effectively as a direct replacement for Retimet™ in some cases.
Copper Foam
- Higher thermal and electric conductivity.
- Best for heat transfer applications.
- Suitable for higher temperatures than aluminum foam.
Silicon Carbide Foam
- Ideal for high-temperature and corrosive environments.
- Best for flow control and diffusion applications.
- More durable in non-impact applications.
Transitioning from Retimet™ to Duocel® Foam
To ensure a smooth transition from to Duocel® foam, we have prepared reference tables to guide customers in selecting the appropriate material based on their specific applications needs:
Aluminum Foam
Flow control, impact protection, diffusion, and air-oil separation
Retimet™ Size: | Duocel Replacement: (Starting Point) | |
10NC | 10 PPI, 10-12% density, 6101 alloy, Heat treated T6 | |
20NC | 20 PPI, 10-12% density, 6101 alloy, Heat treated T6 | |
30NC | 40 PPI, 10-12% density, 6101 alloy, Heat treated T6 | |
45NC | 40 PPI, 10-12% density, 6101 alloy, Heat treated T6, Compressed 1.5x | |
60NC | 40 PPI, 10-12% density, 6101 alloy, Heat treated T6, Compressed 2x | |
80NC | 40 PPI, 10-12% density, 6101 alloy, Heat treated T6, Compressed 3x |
Nickel Plated Aluminum Foam
Used effectively as a direct replacement for Retimet™ in some cases
Retimet™ Size: | Duocel Replacement: (Starting Point) | |
10NC | 10 PPI, 10-12% density, 6101 alloy, Heat treated T6 | |
20NC | 20 PPI, 10-12% density, 6101 alloy, Heat treated T6 | |
30NC | 40 PPI, 10-12% density, 6101 alloy, Heat treated T6 | |
45NC | 40 PPI, 10-12% density, 6101 alloy, Heat treated T6, Compressed 1.5x | |
60NC | 40 PPI, 10-12% density, 6101 alloy, Heat treated T6, Compressed 2x | |
80NC | 40 PPI, 10-12% density, 6101 alloy, Heat treated T6, Compressed 3x |
Copper Foam
Higher thermal and electric conductivity for thermal or electric transfer applications
Retimet™ Size: | Duocel Replacement: (Starting Point) | |
10NC | 10 PPI | |
20NC | 20 PPI | |
30NC | 40 PPI | |
45NC | 40 PPI, Compressed 1.5x | |
60NC | 40 PPI, Compressed 2x | |
80NC | 40 PPI, Compressed 3x |
Silicon Carbide Foam
Flow Control and diffusion for high-temperature and corrosive environment
Retimet™ Size: | Duocel Replacement: (Starting Point) | |
10NC | 20 PPI, Light Density | |
20NC | 20 PPI, Medium Density | |
30NC | 20 or 40 PPI, Medium Density | |
45NC | 40 PPI, Medium Density | |
60NC | 60 PPI, Medium Density | |
80NC | 100 PPI, Medium Density |
Contact us for more details and engineering support in choosing the right Duocel® foam for your application.
By choosing Duocel®, you are ensuring compliance with modern environmental standards while maintaining high-performance functionality in your applications.
Similarities
- Lightweight
- Customizable flow control
- Resistant to high temperatures
- Resistant to harsh environments
- High surface area makes both foams ideal for use in fuel cells and chemical reactors
- Ideal flame arrestor media
Differences
- Duocel’s solid ligament provide a more predictable crush plateau
- Duocel’s solid ligaments provide better heat transfer
- Duocel features adjustable pore size and densities to better control the foams properties
- Duocel® is RoHS-compliant and environmentally friendly!
Why ERG?
ERG has designed, developed, and delivered custom and standardized liquid heat exchangers for over 50 years; including countless high performance heat sinks for a wide range of applications.
With precise adjustments of the Duocel® parameters, we can meet the heat transfer, pressure drop and mechanical requirements for a variety of designs.
ERG has engineering expertise, and design data to model, prototype, and manufacture complete heat exchanger systems. With data-driven internal CFD models, the Duocel® structure can be customized to maximize performance in a given volume.
We have a 50-year history of making quality Duocel® material, certified to AS9100 Rev D, and we’re vertically integrated with a focus on customer service to turn ideas into production parts.